
Improvement of diverless bend stiffener connector

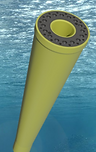

The subsea production scene consists of subsea modules like manifolds and trees, with umbilicals going up to floating production storage and offloading (FPSO) vessels. The umbilicals are pulled up by a cable and attached to a receiving module mounted on the hull of the FPSO. The device that attaches the umbilical to the FPSO is referred to as a bend stiffener connector. Mounted on this connector is a bend stiffener that protects the umbilical from bending motion that could damage its contents.
BACKGROUND

Subsea umbilical
Subsea umbilicals are practically the lifeline of subsea installations, connecting topside and subsea equipment. Umbilicals transfer power, hydraulics, chemicals and optics to subsea trees, jumpers, manifolds, sleds and controls. To reduce strain from waves and ship movement, the middle of the umbilical is suspended from the seabed by using buoys anchored to the seabed. Every umbilical is unique and adapted to the needs of the operation. A pull-in head is attached to the end of the umbilical, which enables the umbilical to securely attach to a bend stiffener connector.
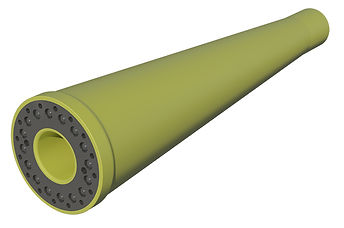
Bend stiffener
Bend stiffeners are mounted on the bend stiffener connectors, with the umbilical being free to move inside it. When the ship moves due to waves or the umbilical moves due to stream forces, the bend stiffener helps keep the umbilical straight so that the power lines, hydraulics and other contents are not damaged.

Bend stiffener connector
The bend stiffener connector is a two-part system for connecting to the topside facility, consisting of a male and a female part. Attached to the inside of the male part is the pull-in head. When the male part is securely connected to the female part, the pull-in head is released, allowing the topside facility to pull to umbilical onboard. Several companies offer various designs to achieve this in quick, secure and cost-efficient ways. Leading products feature either a diverless or a ROV-operated design, as using divers is risky and often more time-consuming.
ABOUT
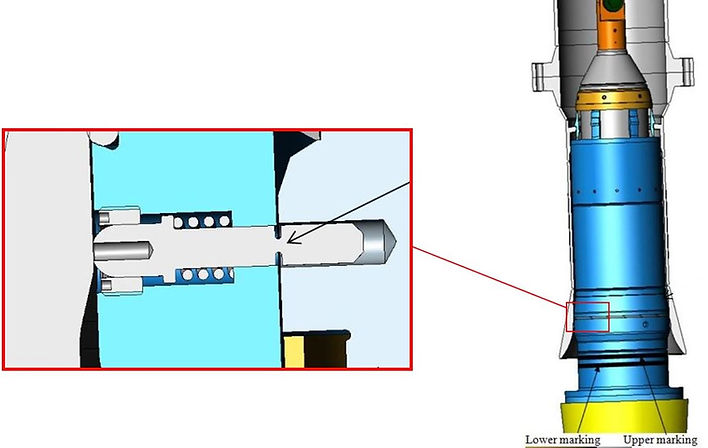
Redesign of shear-pin system
The group was tasked with improving upon a bend stiffener connector with a shear-pin system. For safety and cost-efficiency reasons, the system does not require a remotely operated vehicle (ROV) for the attachment and detachment sequences. For the same reasons the system employs a purely mechanical system rather than hydraulics or electronics.
PROJECT WORK


Autodesk Inventor
​
A digital 3D model was created after a concept was agreed upon. This was then altered as the optimization process was completed. Autodesk Inventor was also used to create an animation of how the new system works.

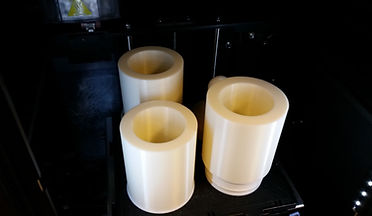
3D printing
In order to conduct a functionality test of the system, a 3D-model was printed. The 3D-model was printed at 18% of its actual size and as a section, in order to see the inner workings of the system. The model was then glued together and spray-painted.
RESULTS

Full system
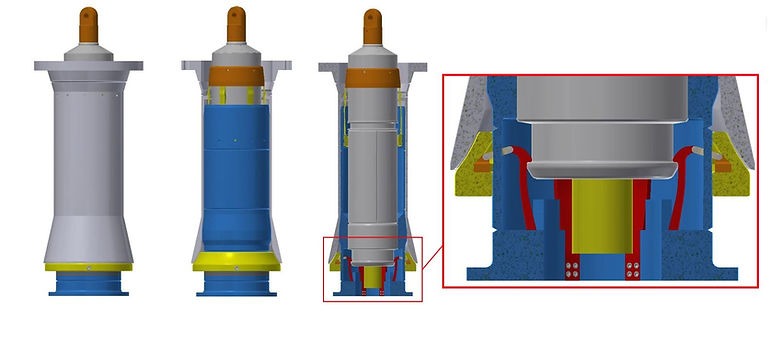
Based on garden hose fittings; the final design takes use of an activation ring, with brackets and hinges that are attached to the hooks. The hooks keeps the pull-in head securely attached to the bend stiffener connector during operation. The system also features an integrated tow-out safety system in the activation ring.
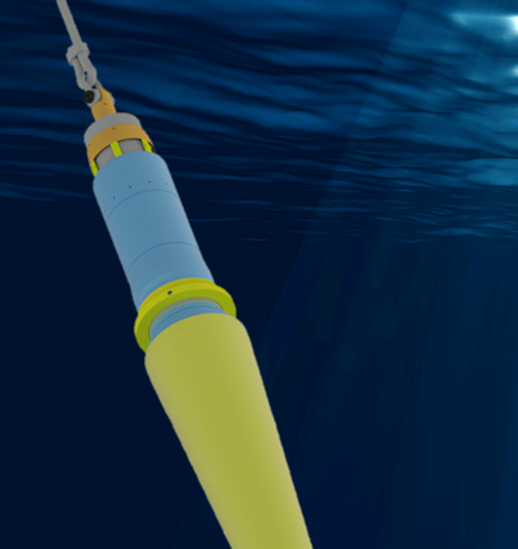
PROJECT PARTNERS
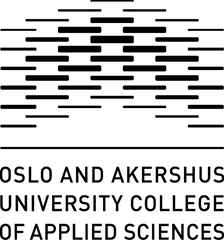
